해외 검사원 자격시험 자료 공유합니다
먼저 영어 공부를 선행하시고 시험 준비하기를 권장드립니다 본인은 일전에 드릴쉽승선해서 검사한 경험있는데 영어가들리지 않아 곤란한경험이 여러번있었습니다
일단 해외자격시험은 국내 자격보다 어렵지 않습니다 다만 영어로 시험이 진행된다는 점이 어려울뿐입니다
API 시험을 치고나서 느낌은?
시험코드는 반듯이 정독해보시고 시험 치세요 대분분의 문제가 해당코드에서 출제 됩니다 그리고 공부방법은 기출문제를 풀어보고 그문제가 어디에서 나오는지 알아야 한다는 것입니다 그것은 추가코드를 공부할때도 마찬가지 입니다 문제를 풀때 앞의 목차를 보면서 어디에서 나올것 같은지 한번씩 생각해 보시기를 추천 드립니다
아직 공유안한 자료들 많이 있습니다 혹시 필요하신분들 댓글 달아주세요 (510,570, 653, ASNT L3, CWI 등...기타 각종 코드 필요하신분들 )
국내 최저가 화상영어 추천(한달 5만원 20회 20분)
국내 최저가 화상영어 (한달 5만원 20회 20분)
국내 최저가 화상영어 추천(한달 5만원 20회 20분) 아직도 말 못하는 수업만 하고 계신가요? ‘영어는 공부’가 아니라 ‘언어’라는 점을 아셔야 합니다 때문에 당연히 원어민과 대화를 하면
qi-inform.tistory.com
1.
a. Remaining life = t actual – t required
corrosion rate
b. L. T. Corrosion rate = t initial – t actual
years between t initial & t actual
c. S. T. Corrosion rate = t previous – t actual
years between t previous and t actual
2. If corrosion rate is not available for new service, it shall be determined within 3 months of service and shall be confirmed by subsequent measurements.
3. MAWP of piping system is worked out on basis of:
MAWP =
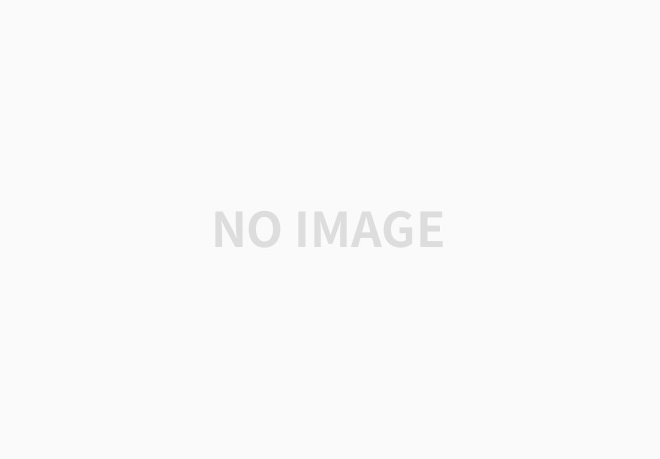
t = t actual – 2 x corrosion loss up to next insp.
For unknown material, assume lowest grade and lowest joint efficiency permitted by the Construction Code.
4. Authorization for repair may be given by Inspector, however authorization for alteration shall be given only after consultation with and approval by piping engineer. After completion, all repairs and alteration work shall be checked and approved by Inspector.
5. A temporary repair may be made by fillet welding a plate patch if SMYS of pipe does not exceed 40,000 psi.
6. Insert patches may be used for repairs if:
a. Full penetration groove welds are provided
b. For class 1 and 2 piping the welds are 100% radiographed or UT checked and
c. Patches have rounded corners 1” min. radius
7. Any welding done on-stream shall be done in accordance with hot tapping checklist as per API 2201.
8. Pre-heating (and maintaining) to minimum 300°F can be substituted as alternative to PWHT for P-1 and some P-3 steels (except Mn-Mo steels). The weld shall be covered with insulation to slow cooling rate.
9. For other steels, PWHT has to be performed as per construction code.
10. Pressure tests are normally required after alterations and major repairs. However, NDE maybe utilized if Pressure Test is not practical, if accepted by piping Engineer.
11. The above grade survey of buried piping shall be conducted at an interval of approximately 6 months.
12. For piping buried in lengths greater that 100 feet and not cathodically protected (CP), the soil resistivity shall be checked at 5 year interval.
13. For poorly coated pipes or pipes with improper cathodic protection, close-interval potential survey shall be made every 5 years.
14. Thickness measurement of buried pipes without CP shall be done at interval of 5, 10, and 15 years if soil resistivity is less than 2000, 2000 to 10,000 and more than 10,000 ohm-cm respectively. Thickness measurement is performed by “intelligent pigging” or by excavation and UT check.
15. Leak testing at minimum pressure = 1.1 x M.O.P. shall be done at half the above intervals for non-C.P. pipes and same intervals for C.P. pipes. Pressure shall not drop more than 5% in 4 hours period (Pressure-Decay Test).
16. Repairs using clamps for buried pipes, the location and date of clamp shall be shown on the marker (flag) and also on the inspection report. Clamp shall be replaced by permanent repair at first available opportunity.
17. All fatigue failure take place due to initiation of surface crack and propagation of crack due to stress fluctuation. There are 3-types of fatigue failures.
If surface cracks are due to stress concentration, weld undercuts, notches etc and stress fluctuation due to mechanical reasons (unbalanced shafts, alternate tension-compression etc.) then it is Mechanical Fatigue. If stress fluctuation is due to temperature swing, it is Thermal Fatigue. If stress fluctuation is due to vibrations, water hammer etc., it is Vibration Fatigue.
18. Corrosion Erosion is due to combined action of corrosion and erosion. It can be reduced by controlling corrosion (by coating or using corrosion resistant materials) and by controlling erosion (by controlling flow velocity, providing harder surface).
19. Caustic embrittlement occurs due to combined action of high caustic strength and higher temperature. It can be controlled by carrying out PWHT and upgrading materials by Nickel alloys.
20. Sulphidation occurs due to sulpher or H2S content in the fluid handled. It can be reduced by using Chromium containing steels as construction materials.
21. High temperature Hydrogen Attack (HTHA) is due to migration of Hydrogen atoms in the carbon steels which combines with carbon in carbons steel at high temperature to form Methane gas (CH4) which collects at grain boundaries causing internal cracks. It can be reduced by selecting the construction materials according to Nelsen Curves. (The material should be above the point of temperature and Hydrogen pressure).
'inspection > API570 시험자료' 카테고리의 다른 글
API 570 핵심 요약 6-6 (0) | 2021.11.27 |
---|---|
API 570 핵심 요약 5-6 (1) | 2021.11.27 |
API 570 핵심 요약 3-6 (0) | 2021.11.27 |
API 570 핵심 요약 2-6 (0) | 2021.11.27 |
API 570 핵심 요약 1-6 (1) | 2021.11.27 |
댓글